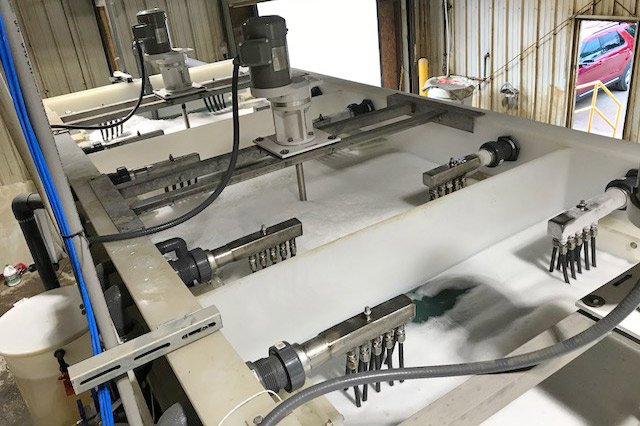
Acid Recovery
Acid Recovery
Utilizing our proprietary, non-stick H2 Conductive Tubing Heat Exchangers, Phoenix’s Acid Recovery Systems offers the best fluoropolymer heat transfer available. Phoenix Systems offers our Phoenix COLD Process and our Phoenix CONVENTIONAL Acid Recovery System.
Efficiency of cooling of any heat exchanger is dictated by the Heat Transfer Coefficient, which is further affected by conductivity, flow intensity, and the coating of the tube surfaces and subsequent crystal build-up.
Our H2™ Conductive Tubing, 2.6 times more conductive than other fluoropolymer tubing, which provides a heat transfer rate similar to steel without the corrosion attack susceptibility.
Unlike other plastic or metal heat exchangers, our non-stick tubing inhibits the build-up of sludge and foulants that dramatically reduce heat transfer efficiency. Our non-stick tubing also allows for easy crystal and sludge removal with either a steam or hot water rinse.
Our design prevents crystal bridging and allows for vigorous fluid flow between the tubes. Unlike small diameter tubing, there is no bundling that restricts flow.
Our heat exchangers are designed to allow for ample spacing between the tubes. For our higher volume plants, we have introduced two new frames with added spacing in length only, or length and width combined.
Heat Exchanger tubing is easy-to-repair and has no weld joints.
Cold Process
Phoenix Systems offers the COLD PROCESS Acid Recovery to further enhance our acid recovery process.
H2CT
Mixing Cell with Stainless Steel Headers
Expected Benefits
Our Cold Process recovers more ‘free acid’ than our conventional acid recovery systems.
Cleaner acid results in reduced chemical consumption per ton of steel processed and more product output.
Colder acid reduces retained iron. Retained iron in return acid of 1.5%-2% (+/-) allows for shorter, more predictable pickling times, which enhances plant output and minimizes over-pickling.
When pickling tank chemistry is optimized, highly reactive clean acid will dissolve scale quickly. The reactive acid will attack the iron oxide portion of the pickling tank sludge and convert it to ferrous sulfate heptahydrate.
Retains “Free Sulfuric Acid” for Re-use.
Process chemistry optimization creates highly reactive acid which dissolves scale quickly for increased product throughput.
Phoenix Systems Control Panel
Conventional ARS
Recognizing that not all plants can take advantage of the Phoenix’ Cold Process, we continue to offer our Conventional Acid Recovery System. Many of the chillers in older plants are only capable of chilled water temperatures of 35°F – 43°F, and finished acid temperature from 50° F – 65° F.
Phoenix Systems Conical Tank and Centrifuge
The Phoenix Conventional Acid Recovery System is a perfect alternative for plants that have time or budgetary constraints. Our conventional acid recovery system still utilizes our H2CT heat exchanger. This heat exchanger offers the benefit of non-stick tubing, which specifically minimizes crystal build-up on the tubing. Crystal build-up on heat exchangers inhibits heat transfer, which negatively impacts acid recovery. Our tubes are spaced for ease in cleaning; no weld joints make stronger tube, and are easy-to-repair.
Flow Meters and Pump